Listen:
Check out all episodes on the My Favorite Mistake main page.
My guest for Episode #94 of the My Favorite Mistake podcast is an old friend of mine from professional circles, David Meier. When I first met him, he had left his career at Toyota, and became a consultant in the Lean methodology around the world. He is co-author of the books, The Toyota Way Fieldbook and Toyota Talent. In recent years, he founded Glenn's Creek Distillery in Kentucky, which I've been able to visit twice. I've interviewed David previously a few times on my Lean podcast — about Toyota/Lean and about the distillery.
Update — His “OCD #5” was named “US Micro Whisky of the Year” in the 2023 edition of the Jim Murray Whiskey Bible. Congrats, Dave!!!
In today's episode, David shares his “favorite mistake” story from his Toyota days and how they created a “no-fault, no-blame culture.”
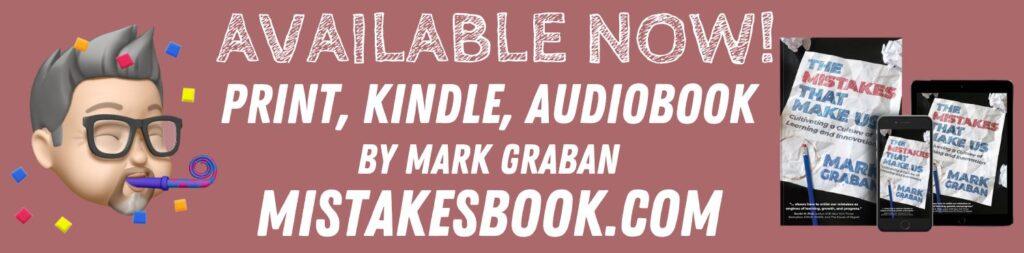
Questions and Topics:
- The Jim Murray Whiskey Bible
- More background about what you learned at Toyota
- Hard for people to talk about mistakes, admitting they’re human
- Blame vs. responsibility?
- Toyota teaches that leaders have responsibility
- Blame with punishment = “accountability”?
- Punishment replaced with learning and improvement?
- Hard on the process, not on the people
- Mr. Yoshino’s mix up with the paint area (Episode #30)
- My episode about the nearly lost episodes (Episode #16)
- Mistakes about mistakes?
- Koko, the gorilla who learned sign language
- Mistakes at the distillery
- Mistakes vs. discoveries?
- Whiskey transported in barrels – mistake or learning??
Follow David on:
Watch the Full Episode:
Quotes:
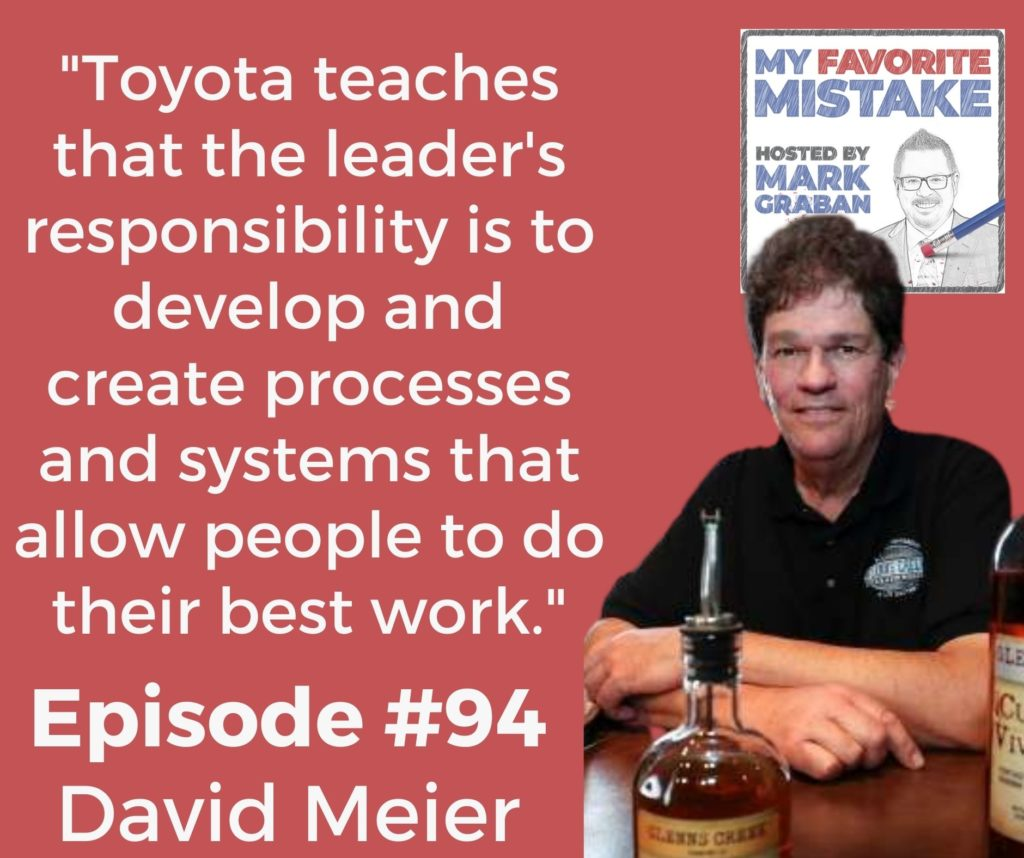
!["Mitigation is probably a better term [than error proofing]. And so, with that in mind, we do have to acknowledge that mistakes are sort of inevitable, but you can apply certain thinking to minimize them in some ways."](https://www.markgraban.com/wp-content/uploads/2021/08/David-Meier-My-Favorite-Mistake-4-1024x858.jpg)
Subscribe, Follow, Support, Rate, and Review!
Please follow, rate, and review via Apple Podcasts or Podchaser or your favorite app — that helps others find this content and you'll be sure to get future episodes as they are released weekly. You can also become a financial supporter of the show through Anchor.fm.
You can now sign up to get new episodes via email, to make sure you don't miss an episode.
This podcast is part of the Lean Communicators network.
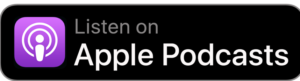
Other Ways to Subscribe or Follow — Apps & Email
Mistakes Working At Toyota And Distilling Whiskey, “What Did We Learn Today?” — David Meier
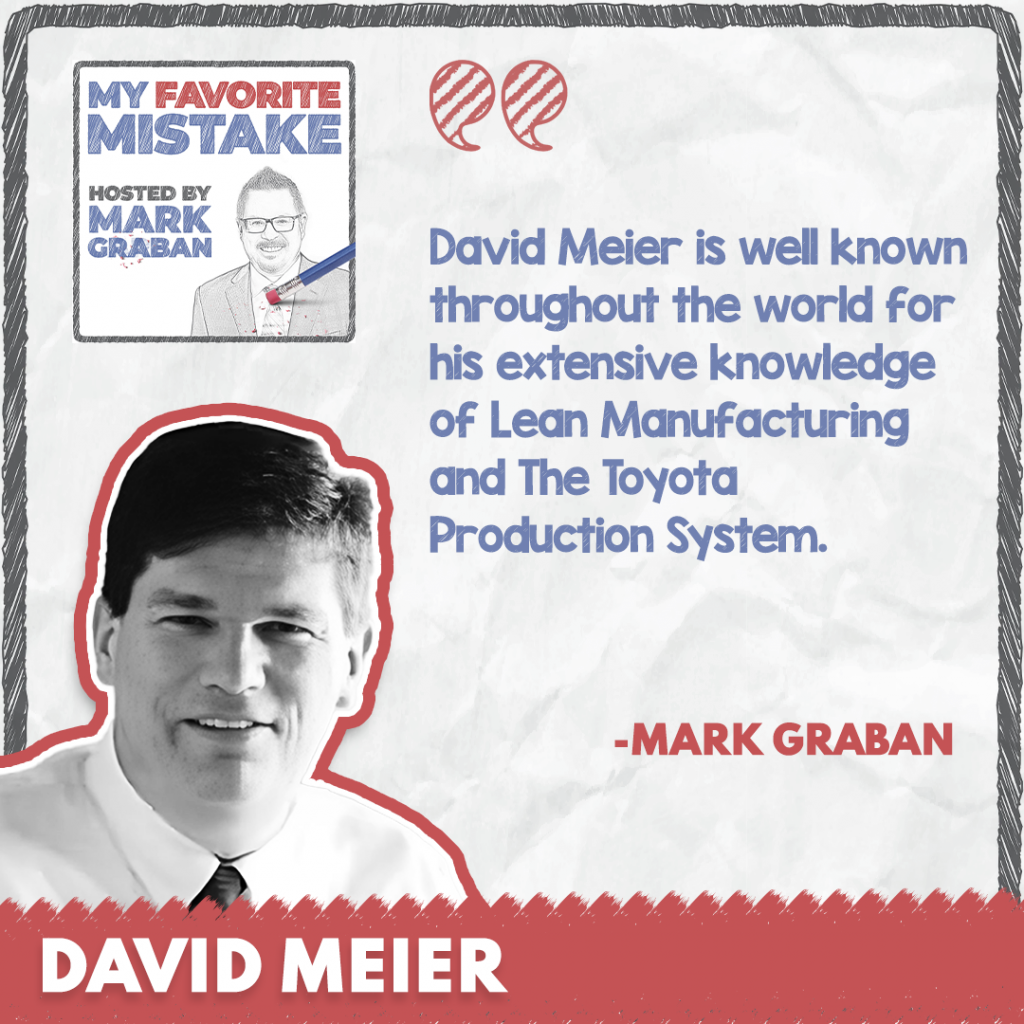
We’re joined by David Meier. David’s a friend of mine. We’ve known each other for several years since we crossed paths. We’ve crossed paths and worked for circles in what I would call my day job or maybe your previous job. Would you still call that type of work that we’ve done the day job, or is that behind you?
I still do a bit of consulting when things come along.
Let me give a little bit more formal introduction to David Meier. We crossed paths after he had a very interesting career at Toyota. He has then worked as a consultant doing similar types of work to what I do. He’s also the co-author of two excellent books. One is called The Toyota Way Fieldbook, and the other one is called Toyota Talent.
This is of particular interest to me. David is the Founder of Glenns Creek Distillery in Kentucky. I’ve had a chance to visit the distillery twice. I enjoy his products very much. I’m going to give congratulations and a shout-out to you that David has gotten real acclaim in the Jim Murray 2021 Whiskey Bible. David, congratulations on that recognition.
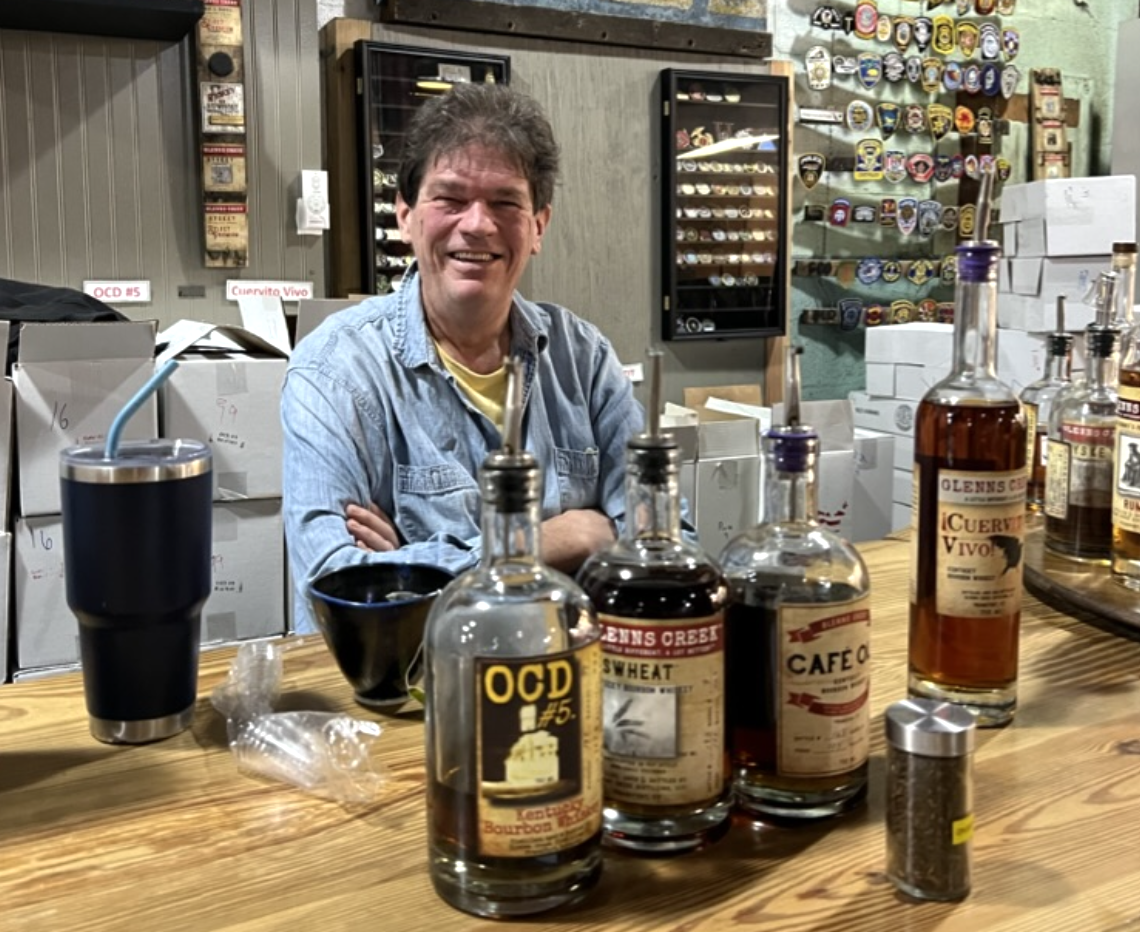
Thank you. I saw that myself. That was nice. Mr. Murray visited the distillery a couple of years ago. It was a good experience.
We’ll come back and talk a little bit more about the distillery and the whiskey. We’re going to talk first about your experiences at Toyota. The regular audience will realize we’re going to deviate from the standard a little bit here. Normally, we jump right into the favorite mistake question. David is going to first tell us a little bit more about some of the backgrounds of what he learned working at Toyota.
When I first saw your blog, I appreciated the idea of being able to talk about mistakes. It’s something that’s hard for people to do sometimes to admit that they’re human and that they can make mistakes. When I started at Toyota, I was 27. I was put into a leadership role there. I had some leadership experience in the past, but certainly not very much.
One of the things that I found frustrating and made me angry was that when my people would make mistakes, the blame came down on me. Toyota operates a no-fault, no-blame culture, but if you listen to any two-year-old kid, they’d say, “It’s not my fault. He did it.” We’re brought up with this idea of finding fault and placing blame. There’s a difference between that and being responsible. Toyota teaches that the leader’s responsibility is to develop and create processes and systems that allow people to do their best work. Certainly, it was hard for me in the beginning with that situation.
[bctt tweet=”Toyota teaches that the leader’s responsibility is to develop and create processes and systems that allow people to do their best work.” via=”no”]
As time went on, I got to understand the difference between responsibility for something and fault or blame for something. Certainly, when you make a mistake, you have responsibility for that mistake. It’s expected at Toyota then that you’re also going to propose some corrective action or something to help prevent that mistake from occurring again.
There’s learning that takes place then.
When one of my people would make a mistake, I’d go out to the process area and I’d look at the situation. Honestly, I’d think sometimes, “How stupid could they be that they don’t understand the correct way to do this?” It took me a while, a couple of years, to be able to clear my brain of any forethoughts about the situation and look at it from a novice’s point of view. Since I was the one who designed it, clearly I understood it. If I didn’t have that understanding, is it that clear to others? The answer is no, not really. You have to understand that when people make mistakes, it’s not intentional. It’s called a mistake. That changed for me.
I have the distillery. When we have a new hire or something, I tell them, “You can’t make a mistake that hasn’t been made here already. We’ve screwed up that. We’ve done this thing. You’re not going to come up with something.” They surprise me and come up with something that hasn’t happened. Everybody goes through this similar learning process. Certain things happen. We don’t want to let any distillate go on the floor, but sometimes, it does. That’s sad.
I was wondering if you could elaborate a little bit. You hear variations of these expressions like, “Be hard on the process, not on the people.” It’s this idea of not blaming the frontline workers. At what point is a frontline supervisor or a frontline leader responsible versus also being part of the system?
That’s exactly what I was struggling with initially. It’s the idea that you have responsibility for process improvement or developing people. It takes a while because of the way we’re brought up. We’re brought up with this mindset. All of a sudden, you’re placed in this different situation. When you’re being scolded, in a way, for what occurred but not blamed, it’s a strange thing to adapt to. It’s clear like, “You have a responsibility. Your responsibility is to ensure these things, do these things, and follow through on these things.” That’s not a criticism per se. That’s an expectation.
There is another thing. Toyota has the process. Out there, we have error proofing, mistake proofing, or whatever you want to call it. I tune in to your episode about almost losing those recordings. You talked about backup and so on. At one point, you said it’s virtually fail-safe or something to that effect. I would say, “Nothing is.” You’re going to acknowledge that and get a solid-state drive. It’s certainly more robust than a spinny drive. There is no actual error-proofing.
In problem-solving, Toyota uses the word countermeasure. If you understand that term, it has to be deployed continuously in order to be effective. I always tell people, “If a human puts a system in place, another human can work around that system, bypass that system, or shortcut that system.” The idea of air proofing isn’t to eliminate the error. It’s to make it more difficult to make a mistake. It’s not possible to eliminate mistakes.
You might use a term like error mitigation instead of error-proofing. That sounds very absolute. Maybe there are simple cases where you can error-proof something.
I would beg to differ on that because you can always bypass something. If it’s possible for a human to invent it, it’s possible for a human to circumvent it. Mitigation is probably a better term. With that in mind, we do have to acknowledge that mistakes are inevitable, but you can apply certain thinking to minimize them in some way. In some cases, it’s not possible to apply something or it’s certainly not easy to apply something.
[bctt tweet=”Mitigation is probably a better term than error-proofing. With that in mind, we have to acknowledge that mistakes are inevitable, but you can apply certain thinking to minimize them in some ways.” via=”no”]
You used the word responsibility. There’s a different ability word that comes to mind. I hear this way too often in healthcare. It’s not exclusively a healthcare thing, but it’s common in healthcare. The word accountability gets thrown around and gets weaponized. It’s like, “We’re going to hold people accountable,” which is a polite way of saying, “We’re going to blame them, and we’re going to punish them.” Was part of the difference at Toyota that scolding or what felt like blaming? Was the punishment replaced with learning and improvement?
That’s a very good point. That’s a point that I often make. They want to make accountability this way. They’re like, “You need to be accountable.” I say, “Accountability goes this way. I need to be accountable. Can you help me be accountable? We’re in this together. If I agree that I’m going to live a certain way or behave a certain way and you experience me not behaving that way, then you help me be accountable.” I agree with you. They’re weaponizing it. They’re like, “Here, fill out this paper to agree that you understand this situation. If you fail to do this, then we can punish you and get what you deserve.”
The word accountability, going back to the root words, means to give account, which is about explaining. It is different than the notion of responsibility. That root of accountability wasn’t meant to imply blame and punishment. You can explain what happened. That’s a healthy thing to figure out. You mentioned the episode where Jamie Parker interviewed me about the episodes I almost lost. That was episode sixteen for people who want to go back and check that.
You mentioned the episode with Katie Anderson and Mr. Yoshino. It was episode 30 for people who want to go back. Mr. Yoshino told a story about being very young and early in his career at Toyota and he made a mistake. You could call it a slip-up. He grabbed the wrong container of something in the paint area and it caused a problem. It sounds like that error was too easy to make. What was your reaction to that story?
That’s exactly when I decided to reach out to you because my mistake is very similar to that one. I related to it quite well. When he started talking about that, I said, “I’ve been there, done that.” I’ll launch into it for you. The first thing is this wasn’t my mistake. One of the things I try to explain to people is that at Toyota, or your explanation of Swiss cheese, a lot of things have to line up sometimes for the “mistake” to occur. If all of them don’t line up, then the mistake didn’t happen. You maybe had a near miss. This is one of those cases. This was about 4 to 5 years into my Toyota experience. We weren’t newbies at that point. One morning, my team leader came up to me. I could see him white-faced. Something wasn’t right. He says, “The bumper core process is powder.”
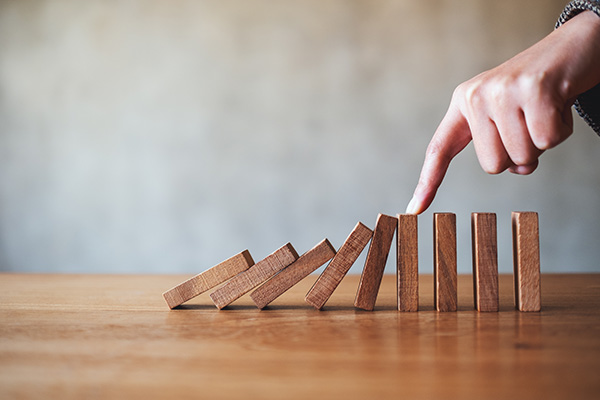
What does that mean?
This is supposed to be the energy absorber they called in the vehicles back then. It was a polyurethane hard foam piece, not powder. I walked over there with him and took a look at the situation. Sometimes, you experience something that is so far beyond your realm of experience that you can’t process it. It would be nothing like the typical defects that we experience or that we deal with day in and day out. This was so far out of that realm that I blanked.
At Toyota, you understand some things. One of those things is you have about an hour’s worth of work in process inventory between you and the next process. In that case, it’s bumper paint. Bumper paint has about an hour’s worth of inventory between them and the assembly line, so you got about two hours before everything stops. That’s number one. You immediately call the managers, maintenance, engineers, and everybody to come down to the problem area.
In retrospect and looking back on it, sometimes, you’re experiencing something that’s so far beyond the realm of your possibilities that you don’t know what to do. Everybody puts their heads together and says, “Let’s take this action. We’ll drain the chemical system, refill the system, start from scratch, and see how it goes.”
This process alone to drain this system, you’re talking an hour or so. We’ve never done it before. It’s never had to happen, so we don’t know. You got to fill it up, and then the chemicals have to blend, and so on. You’re 2 or 3 hours into this thing before you can even have an effective chance at a countermeasure. To make matters worse, once you pour these parts into the mold, it goes through a heating cycle that takes about eleven minutes. I would say it’s like when the astronauts go to the other side of the moon. You’re sitting there waiting, hoping, and praying that these parts are going to be okay after all this work.
The mold comes around, opens up, and powder again. It was crumbly powder. We’re all scratching our heads. You have to understand one thing here. In addition to those of us who had been with Toyota for years, we had a lot of seasoned Toyota veterans from Japan working with us at that point in time. They were 20 to 30-year guys, and nobody had experienced anything like this.
The decision was made this time. Maybe the automated system was messed up somehow and it wasn’t putting in the right material and so on. We were like, “Let’s drain it all down, and then we’ll refill it manually,” which had never been done. We were like, “We got to get the manual out and figure out how to make that happen.”
Several more hours go by. This happened to me on more than one occasion at Toyota where the process was down for quite a long time. You look up and all of a sudden, there are 25 people from all over the plant. The manager from every department comes because they all want to know, “What are we going to do with our people? How long might this take?” Everybody comes together. You have 25 new friends that you didn’t know about before.
We go through this whole process of redoing it all manually. It’s the same thing. We put it in the mold and it goes in the oven for eleven minutes. You’re waiting, and then the mold opens up and it is powder. We’re 6 or 7 hours into this. When the line stops, everybody understands the significance of that. Everybody is doing their best to try to get it resolved. At that point, people are wandering around, looking, and trying to think, “What else could it be?”
From my recollection, off to the side, I hear somebody say, “What do you do with methylene chloride?” My ears perk up. I’m like, “What?” I was familiar with methylene chloride because of my previous job. I worked as a safety coordinator and I had to deal with the chemicals and so forth. We had no use for those in the plastics department. No methylene chloride was needed anywhere that we did. I immediately went over to where he was and said, “What are you talking about?” He said, “There is a drum here that says methylene chloride on it.” I said, “We’re putting a solvent in where we were supposed to be putting a catalyst in.” Instead of solidifying the material, it was degrading material.
In the end, we had to do an analysis and problem-solving. Mr. Cho, our president, asked one question, which was, “What did we learn today?” The thing about it is the mistakes that led to the line stop or the downtime weren’t the big mistake. The big mistake, which took me about ten years of reflection to understand, was what took us so long to figure out what caused the issue.
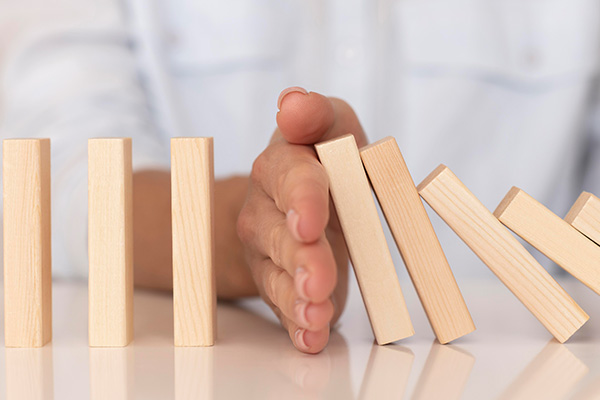
It was seven hours in, and we missed one of the most fundamental lessons when a problem occurs or when a mistake happens. It is one of the fundamental lessons which we had been taught over and over at Toyota. To analyze the mistake, what happened? You could do a five why’s and say, “Somebody put the wrong material in the system. Why? It’s because the wrong material was delivered. Why? It’s because it was in the wrong location.” Who knows? It could have been a mistake on the shipping and bill of lading or where they stored it at oil stores. The drum was the same color, the same size, and the same manufacturer. We know things like expectation bias get in the way. It looks normal.
This sounds like some medication errors.
It’s the same thing. It looks normal. It doesn’t look out of place. We walked by it all day long and failed. It took me a long time to understand where we failed. The thing about it is, in that case, all of us there failed in the same way. I’m not talking about 2 or 3 people. I’m talking about 20 to 25 people. These were experienced people who should know better.
The failure was we didn’t verify the standard. Nobody thought to say, “Let’s go and check all the chemicals that we’re putting in the system. Let’s switch them all out and put a fresh batch in.” It’s the feeling we got latched into, and this happens a lot, too. It’s where you latch into one possibility, and it must be the blending system. It wasn’t about what we put in the system. It was about the system itself.
That seems like that’s a form of cognitive bias. I’ve heard others talk about how the first solution that people come up with, we tend to lock in or gravitate too strongly toward that one. Even if we’re trying to brainstorm multiple possibilities, our brain tends to stick with the first one. That’s at our own risk.
It’s extremely common. Particularly in that scenario where we were faced with a situation that was so far beyond anything that we could imagine as a cause. With your everyday defects or everyday situations that you’ve dealt with before, you go back to what you know. In this case, it was too far out there. As I recall, there was a list drawn out about what could be going on and so forth. We didn’t go and look and see what all the materials were or whether were they the correct materials. That’s a fundamental thing. Step number one is to confirm that what you’re dealing with is what it’s supposed to be.
There might have been a bias or an assumption where people might have thought such a fundamental error like that wasn’t going to happen. It must be something complicated instead of something simple.
That’s a possibility as well. Visually, that drum was the same color, the same size, and the same manufacturer. From several feet away, it didn’t look out of place. It didn’t look abnormal. It didn’t look like something was wrong. Still, it was the idea when it finally occurred to me that we all fundamentally failed to do the most basic thing, which is to confirm.
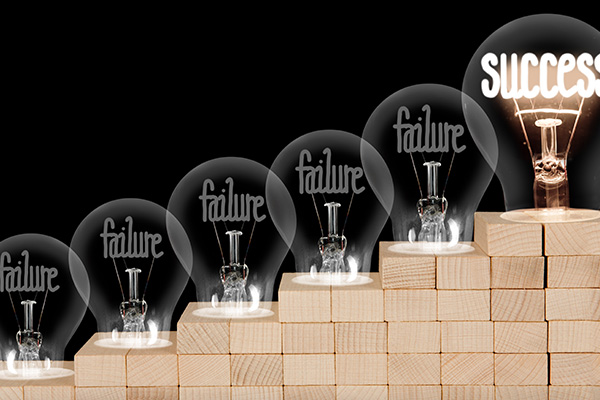
With expectation bias or confirmation bias, you’re right. Those are things that often get in our way when we’re trying to resolve a situation or avoid mistakes. A lot of mistakes in healthcare are common. The expectation bias says, “I’m working with Mark. Mark is a good guy. I trust Mark, so I don’t need to double-check on what Mark did because he’s a good guy.” It’s a very common phenomenon in the realm of making mistakes.
You mentioned it took quite a long time for this to come together in your mind. What triggered that learning or that recognition of the memory of that, and then the recognition of the mistake within trying to figure out the mistake?
It’s what I call the bigger mistake because if we had checked and confirmed things, we could have resolved it within the first effort and drained the system because clearly, it had contamination in it. We could have refilled it with the correct things and probably be back to normal hours sooner. Back then, certainly, I was not as experienced as I am now. I became later when I finally understood it.
We sat down and did what people do with problem-solving. We were like, “Why did the wrong material end up in that place? What mistake was that? What can we do to make sure that mistake doesn’t happen again?” I don’t think anybody ever asked the question, but I learned this later. It’s to say, “How can we resolve problems more quickly? How can we get to effective countermeasures faster so that we don’t experience the length of doubt?” We focused on the mistake, which was putting the wrong chemical in the wrong place.
Many organizations would’ve gone down the path of, “Who put the wrong chemical into the machine?” They might go down that path of, “We’re going to write them up or punish them.” That’s not as effective of a path to learning, improvement, and ultimately, the success of the team, the plant, or the company.
We did not have a process in place that said to the operator, “Verify the chemical before you stick the hose in it.” That was one of the corrective actions that took place. To make matters worse, the individual who did it was temporary. It was summertime. We would hire children of workers from college or whatever to come and fill some jobs in the summer. It was the Swiss cheese. It wasn’t the final act of putting it in, certainly. It was also the delivery of the wrong thing. It was also the pickup of the wrong thing. Who knows how far back the series of mistakes went?
You were saying earlier about error mitigation, or it might be very imperfect, or people can work around a system. If it’s dependent on someone double-checking the chemical, they might forget or be distracted, or there might be some other human factor that gets in the way.
In any good system like in aerospace or whatever, the more critical it is, the more redundancies you want to have. We had multiple redundancies, and they went back all the way to oil stores, which is where the chemicals were received in the plant and then delivered to us. The person who said it there had to confirm it. The person who was to put it in the machine had to confirm it.
If I recall, we got the supplier to change the color of the drum so that it didn’t match methylene chloride or whatever. All of those countermeasures were fine. Later, I realized, “Why did we fail at this fundamental lesson that says, “When something isn’t working right, go back and verify the conditions, the parameters, or whatever?” Verifying the standard is the first thing. If you find something that’s out of standard, you put that back in standard and go from there. It’s surprising because there were so many people involved who all fell into the same trap.
I appreciate you sharing that story and the broader reflections from Toyota. I want to bring the conversation back to Glenns Creek Distillery and the work that you’ve been doing there. David and I have done interviews in my Lean Series where we take a real deep dive into what he’s doing there. I’ll point to that.
I don’t know if this was a mistake or a discovery. Maybe this was an urban legend. It’s the idea that bourbon was transported down the Mississippi River and was put into oak barrels for the purposes of transportation. It was discovered that the time spent in the oak barrel changed the whiskey, taking it from a clear distillate to something with more flavors and color. That could have been framed, whether that story is true or not exactly. What might have been a mistake in transportation? They didn’t use an inert stainless steel container if that even existed at that time. A “mistake” led to the creation of a lot of value through that learning and that discovery.
I’d go way back in human history and say that mistakes, things, or whatever you want to call it led to a lot of new things. My guess is that humans discovered that sprouted seeds were fermented. That’s because this sprouting of the seed releases enzymes that then converge starch in the seeds into fermentable sugars. To discover that, you probably had sacks of grain that got wet accidentally, and then sprouted and started fermenting. You saw animals eating that fermented stuff and having a great time. You put two and two together and say, “Let’s do this.”
[bctt tweet=”Mistakes can lead to a lot of new things.” via=”no”]
The story you’re referring to is more of an urban legend. There are a lot of legends like that in this industry. Who’s the first distiller? Who first did this? In fact, liquids were stored in oak containers well before the United States was the United States. If you see any of these old shows or whatever, you’re going to see wooden barrels all over the place because that was the way everything was transported. Not only did they not have stainless steel, but they didn’t have plastic or cardboard.
You had two different kinds of barrels. You had dry goods barrels that didn’t have to hold liquid, and you had liquid-type barrels. It had anything liquid like wine, honey, or molasses. Whiskey would’ve been transported in a barrel. The difference was barrels for wine, for example, are typically toasted but not charred. The charring process lends a lot to the burb. It gives it a more amber-ish color and certainly some smoky flavors perhaps and so on.
That legend can’t be validated. Elijah Craig was a tight wad, and he had a pickle barrel or sardine barrel or something that’s liquid. He wanted to reuse it, so in order to get rid of the flavor, he burned the inside of it and created good whiskey. It’s a tall tale. The French, as I understand it, were charring barrels and storing whiskey in barrels years before.
Scottish readers may claim some right of first discovery to some of that.
I don’t think they used charred barrels. Tens of thousands of years ago, the Vikings discovered that white oak was pretty good for making boats because it kept liquid out. I’m sure then people realized you could use it to keep liquid in as well.
Maybe this is the final question before we wrap up. Can you think of an example in your distillery operations where you’ve got maybe not mistake-proofing but an error mitigation strategy in place? You said you’ve made a lot of mistakes already, but what prevention do you try to put in place?
A lot of what we do is manual in nature. When you have manual things, it is a little bit more challenging to put in error-proofing. What I try to do in that case is build the step into the standard work. For example, when you’re going to fill the still, you have to drain the still and certainly want to make sure that the valve is closed. We could automate that. I could put actuators in there and have all that automated, but that’s expensive. It’s an easy enough task, but it happens sometimes. You learn and say, “Step number one, close the valve. Step number two, when you get ready to turn on the pump to put something into the still, look over and double-check the valve.”
One of the things they taught us at Toyota is Yoshi. It means to check or confirm. When I train someone, I say, “I want you to point at that thing so that I understand that you’re doing what you’re thinking in your head.” A lot of mistakes occur because our brains are sidetracked or on another thought. In certain situations, you fall into hypnosis because of repetition.
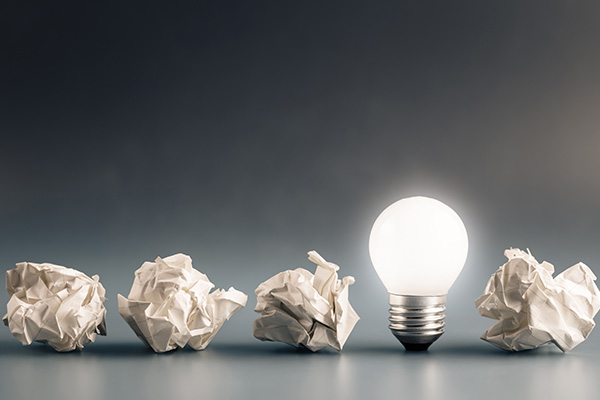
What happens at the distillery is what we call getting squirreled. You’re in the midst of a task and something else requires your attention. You go away from the task, and then you come back and miss a step. After the startup, I say, “Double-check everything all the way around.” We do have some more automated error mitigation things, like alarms and things, to tell us that something needs attention or so on. We continue to try to incorporate those whenever a mistake is made.
Such as in life, mistakes are made. Hopefully, they’re not big, expensive mistakes like shutting down an assembly line for a long time or dumping a barrel of whiskey.
I tell people in healthcare, “If somebody makes mistakes, the consequences are huge.” That situation at Toyota roughly was about an $8.3 million loss, but a loss of life is worse. The consequences are more severe. In those cases, you have to be even more diligent about applying some thinking to minimize the possibility of mistakes and mitigate them. It is part of life, unfortunately. It is part of being human. We can look at all kinds of situations where there were redundancies in place, and the outcome still occurred.
You hit it on the head. It’s ineffective to punish somebody for failing because we all fail. We talk about this a lot. Certainly, people in the audience will raise their hands and say, “Sometimes, people are irresponsible. Sometimes, they need to be punished.” I say, “If I look at a person and they make some significant amount of mistakes more than somebody else or outside some normal range, then maybe that person isn’t fit for the work that they’re doing or they need to do something else.”
At Toyota, the idea was if you make a mistake, I’m going to ask you what you think about that, how you can minimize that, what was going on in your head at the time, and what things can we do to try to minimize that from happening. I had worked with one guy one time. This was after Toyota when I was consulting as a manager. He had this fundamental belief that if people had to fix their own mistakes, they wouldn’t make those mistakes again. I said, “They might not, but what about the next guy? What about the next person who comes into that position? How’s that thinking changing anything? All you’re doing is saying, ‘If you fix your own mistakes, you won’t do that again.’”
That sounds like the equivalent of putting a dog’s nose down in poop on the floor. I don’t know if that’s effective. It might feel like it’s doing something. You might feel better, but no.
I’ll come full circle. Those are the same things that I had to adapt to, understand, and come to terms with my own self. I certainly had those urges as well to punish, to retribution, or something. It’s embedded in us. It’s around us. It’s in our culture.
Arguably, that blaming is human nature. You can go back to the story of Koko who passed away a few years ago. There was a gorilla that trainers and researchers taught American Sign Language. There’s a famous story about Koko where Koko had a real, live pet kitten. She loved it and took care of it. There was some day when the researchers came back in and there was a sink fixture that had been torn out of the wall. There’s only one explanation for what happened. They asked Koko, “What happened?” The story goes that Koko said in signed language, “Cat did it.” That’s what I’m saying. We’re somehow wired. It must be an evolutionary survival tool. If you can pin blame on someone else and somehow survive, your genes carry forward.
We do the best we can to create cultures where we’re focused on fixing the process instead of blaming people. To me, that’s one of the lessons that I’m fortunate to have learned from the former Toyota people I’ve worked with and been mentored by and through my own work and experience. Like a lot of things, it’s a hard habit to break.
Maybe I’m going to go pour some of your whiskey. That’s a habit that is one I’m not trying to break. It’s a good one. David’s products are produced at Glenns Creek Distillery. The website there is GlennsCreekDistillery.com. For people who are looking to possibly buy and try your whiskeys, can you tell people a little bit about the distribution and what parts of the country they might be able to find you?
First of all, don’t blame me that we can’t ship. I don’t make the laws. I have to follow the laws, and people misunderstand those all the time. We’re small, but we’re in four states. Those are Kentucky, Tennessee, Wisconsin, and Michigan. I know it’s not enough yet. We get requests from people all over the place for them. We’re doing the best we can. We’ve grown and expanded production. We turned one happy mistake into something. We ran out of rye once, which is one of our secondary grains. John asked a question, which was, “What would happen if we made 100% corn bourbon?” Usually, I say, “I don’t know. Let’s see. Let’s try. Let’s do an experiment.” We have what we call cob corn-only bourbon that is aging. Hopefully, we’ll be able to release that shortly. It was born out of a mistake.
That’s interesting. When things get back to normal and when I’m in that part of the country, I’m going to come to see you again and hopefully get to pick some of that up and try it. My favorite of your whiskeys is the Café Olé product. That was intentional. That was not a mistake, right?
That’s correct.
It turned out great. This episode has turned out great, so thank you for that. Our guest has been David Meier. His books, which I like a lot as well, are The Toyota Way Fieldbook and Toyota Talent. He co-authored with Jeffrey Liker and again, it’s Glenns Creek Distillery. Someone could combine the two. They can pour whiskey and sit down with a book next to the fire. They can read, learn, have a sip, and reflect. Thank you for helping us combine those worlds a little bit in the discussion here.
It’s always a pleasure. Thank you
Thank you.
—
Thanks again to David Meier for being our guest. To learn more about him, his distillery, his books, and more, you can go to MarkGraban.com/Mistake94. As always, I want to thank you for tuning in. I hope this show inspires you to reflect on your own mistakes, and how you can learn from them or turn them into positive ones. I’ve had the audience tell me they started being more open and honest about mistakes in their work. They’re trying to create a workplace culture where it’s safe to speak up about problems because that leads to more improvement and better business results. If you have feedback or a story to share, you can email me at MyFavoriteMistakePodcast@Gmail.com.
Important Links
- The Toyota Way Fieldbook
- Toyota Talent
- Glenns Creek Distillery
- Lean Series
- Episode 16 – Mark Graban on His Recent Mistake That Almost Lost Four Episodes
- Episode 30 – Leadership, Learning, and Culture: Mistakes and Insights with Isao Yoshino and Katie Anderson
- MyFavoriteMistakePodcast@Gmail.com
- https://www.LeanBlog.org/2018/06/Podcast-309-David-Meier-Bourbon-And-Continuous-Improvement/